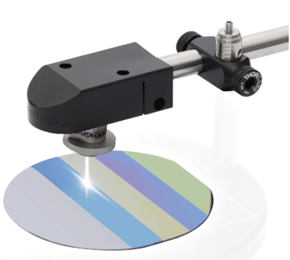
半導体製造ラインで必須となるのが、エッチング工程です。その際に重要となるのが、膜厚測定です。エッチング時に膜厚か均等になっているかどうかで製品としての品質が決定します。
目次
半導体製造において、こんな課題ありませんか?
膜厚測定はエッチング処理後に測定することが多いものの・・・
半導体製造ラインで必須となるのが、エッチング工程です。
通常の場合、触診式段差計や電気的な測定によってシリコン酸化膜等の膜厚測定は、ほとんどエッチング処理後に行います。
しかしエッチング処理後の膜厚測定には、大きく2つの問題があります。
- 成膜時に生じた誤差の原因特定がしづらい点
ナノレベルの膜厚測定では、温度や振動、歪みなど、様々な要因を考慮しなければいけません。エッチング処理後では、どの段階でどの要因によって成膜誤差が生じたのかを特定するのが困難になります。 - 再現性が高い膜厚測定ができない点
膜厚測定はエッチング前後で同じ場所を測定することで評価するのが一般的です。しかし チャンバーからの出し入れを行うと、同じ場所を探すのが困難になるだけでなく、セッティング誤差が大きくなってしまうために正確な膜厚測定をすることができません。
膜厚測定はインラインで行う方が正確に測定できます!
- 成膜誤差の特定が容易に!
エッチング装置内で膜厚測定することで、成膜誤差の要素をプロセスガスのレシピ等に限定することができます。 - 再現性抜群の測定結果!
インラインで膜厚測定をすることで、同じ場所を何度測定しても、10nm~10μm程度の膜厚であれば0.1nmの再現性を出すことが可能です。
上記のような理由から、膜厚測定はエッチング処理後ではなく、インラインで行う方が正確に測定できるのです。
高精度なインライン膜厚測定はお任せください!
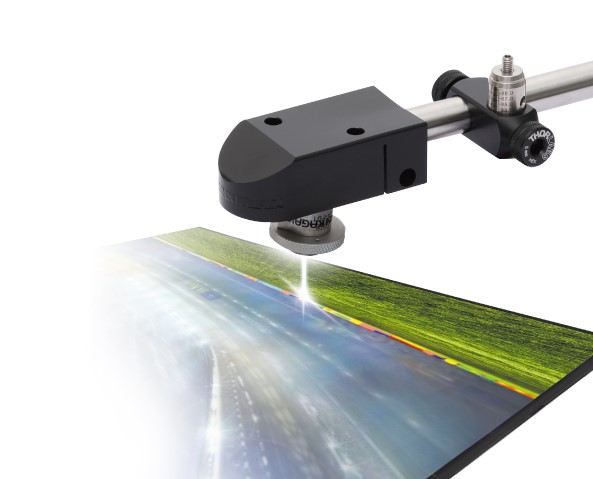
当社で取り扱っている「反射分光式膜厚モニタ」なら、インラインでの膜厚測定を高精度に行うことができます。
インラインでの膜厚測定時に重要となるのが、ステージ性能です。
- 高精度ステージで面内バラつきを抑制!
他社製品を凌駕するステージ性能で、より正確な測定を実現します。 - エッチング以外の工程にも対応!
ウェハ研磨(CMP)工程でのインライン終点検出センサや、リソ工程でのスピンコータでのレジスト塗布の終点検出センサとしての使用実績もございます!
半導体の膜厚測定にお困りの方は、当社までお気軽にお問い合わせください。